(西安工业大学,陕西 西安 710032)
摘要:利用Ansys有限元分析软件对2SFZ14—21手动扁式单闸板试油防喷器的主壳体在额定工作压力和强度试验条件下进行了分析,得出了构件在受载后的应力分布及危险点,在分析的基础上对构件的几何结构进行了两次改进及优化,消除了构件上的应力集中点,降低了最大应力值,保证了设备的可靠性和安全性。
关健词:单闸板防喷器主壳体;有限元分析;优化设计
中图分类号: 文献标识码:A 文章编号:1672—545X(2007)02— —
2SFZ14—21手动扁式单闸板试油防喷器为海上石油平台设计的一种防喷器,其结构形状复杂、工况条件恶劣,还没有专门的设计计算规范。为验证其设计的合理性和安全性,笔者采用Ansys8.0分析软件对该防喷器的承压主壳体进行了有限元分析计算,给出了额定工作压力和强度试验压力条件下的单元应力数值及云图,并按照压力容器规范对有限元计算结果进行了分析讨论和强度验证。
有限元法起源于20世纪50年代的结构矩阵分析法。有限元法通过对连续系统的离散化来求解系统的应力和应变等。随着计算机软硬件的飞速发展,有限元方法在在各行各业得到广泛地应用,尤其是在机械设计行业。常见的有限元分析软件有:Ansys、Nastran、Marc和Algor等。本文就一般设计过程来讨论有限元方法的应用,不涉及软件的具体使用技巧,同时从工程应用角度考虑,注重经济和实用,考虑效率和成本。
1 防喷器主壳体的建模、初步分析及优化
防喷器主壳体的建模、分析及优化过程如下:1)建立几何模型;2)确定载荷及加载方式;3)进行有限元分析;4)通过对分析结果的观察,综合运用力学知识和经验判断,提出下一步试探“优化”模型进行再次分析直至达到满意的结果。
1.1 主壳体初始模型描述及基本假设
主壳体是防喷器中的主要承压零件,采用合金钢锻件整体加工而成,上、下部为KY250和CQ350法兰连接,它与闸板通过螺栓连接。由于主壳体上下对称,计算时取其中一半进行受力分析以减少计算量,主壳体材料为合金钢,弹性模量E=2X105N/mm2,泊松比μ=0.29。为了能够提高运算的效率,在不影响结果的前提下我们可将部分元素简化。在Ansys软件中进行模型的简化,也就是将模型进行修补或删除。在这里就主壳体而言,可将法兰盘上的圆角、闸板体导轨上的槽、孔的倒角以及部分倒角简化。我们预置设计目标是:期望其最大应力值小于 7.0×107 N/m2(即至少10倍左右的安全系数)。
1.2 主壳体初始模型受力分析
运用软件进行有限元分析的一般过程如下:
1) 按照实际形状,用三维CAD软件(或有限元软件自带的前处理器)建立三维实体几何模型(本文中考虑到Ansys建模功能不是十分强大和Pro/E与Ansys良好的接口技术,故应用Pro/E进行建模);
2) 在有限元软件环境下建立分析数据库,导入三维实体几何模型,建立有限元模型数据库;
3) 加入材料信息;
4) 指定有限元网格类型进行单元格划分、加入约束和载荷(如图1);
5) 指定分析类型;
6) 进行后处理并显示结果。
按照以上过程,对主壳体初步分析的位移图(如图2)、应力图(如图3)。
通过位移图、应力图得知,最大位移和最大应力都出现在了主阀体与闸板总成轨道相贯处,最大位移0.04861㎜,最大应力132.145 N,这和实际实验中观察到的结果是相符的。
图1 边界约束及加载 图2 位移图
参考零件受力方向和零件受力后的几何形状分析:1)最大应力远小于材料的屈服强度785Mpa,但还没有达到我们预先设定的期望值;2)最大应力产生在阀体内腔与闸板总成轨道的相贯处;3)由力学知识知道,弯角处应力集中。综合以上分析得出下一步优化方案:为了避免此类问题的出现,可将相贯处进行圆弧处理,以减少应力集中;又由于孔的内径为140㎜,所以在加工的时候也是容易实现的。
1.3 主壳体模型第一次修改及分析
按照前文分析对模型几何形状作修改,修改后形状如图4,对修改后的有限元模型重新划分网格,运行分析结果如图5、图6。
图3应力图 图4 修改后的构件图
图5 构件修改后的位移分析图 图6 构件修改后的应力分析图
观察结果:1)把图3与图6进行比较发现,该零件整体应力明显地下降了;2)最大应力点也有所偏移,减小到99.044 N;3)这个结果已经很接近我们的期望值,但还是没有达到我们需要的满意程度。
分析下一步优化方案:在图中我们能够看到应力虽然有所减小,但是出现了应力的偏移,从位移图中可以看到薄弱环节仍然存在。
2 主壳体模型第二次分析并优化设计
对相贯线进行圆弧处理后,该处的最大位移和最大应力得到很大的改善。但是应力集中转移到闸板总成轨道的内壁上,通过改进分析后发现最大位移出现在了椭圆形孔上。
现在重点对最大位移处进行计算分析,工作压力25MPa作用在内壁上,这里取受力过程中的最大截面,并且承载的壁厚取最薄处30 ㎜, 长为160㎜(图7)
图 7 椭圆形孔承载情况简化图
截面上所受压力为
p=PA=25×106×160×160×10-6=640 KN 式(1)
由平衡方程得支反力为
RA=RB=320 KN 式(2)
载荷集度 KN/m 式(3)
由平衡方程ΣY=0和ΣM=0,求得:
式(4)
式(5)
依照剪力方程和弯矩方程作剪力图(8)和弯矩图(9)
图8 剪力图 图9 弯矩图
最大弯矩的绝对值12.8KN/m,出现在截面的中心位置,与ANSYS分析的结果相同。现在用积分法求弯曲变形(如图10),挠曲线近似微分方程:
式(6)
图10 挠曲线图
将式(5)积分两次得出:
式(7)
式(8)
由于A、B两处的挠度等于零,故 x=0时 =0
因为截面上的外力和边界条件都对跨度中点对称,挠曲线也应对该点对称,因此,在跨度中点挠曲线切线的斜率 和截面的转角θ都应等于零,即 x=1/2时 =0
把以上两个边界条件分别代入 和 的表达式,可求出
于是得转角方程及挠曲线方程为
式(9)
式(10)
在跨度中点,挠度曲线切线的斜度等于零,挠度为极值,由式(10)得
式(11)
在A、B端,截面转角的数值相等,符号相反,且绝对值最大。于是在式(9)中分别令x=0和x=ι得
式(12)
其中I为惯性矩,矩形的惯性矩 b为宽度 h为厚度
则 , 式(13)
当 h=30㎜
㎜
当 h=40㎜
㎜
当 h=45㎜
㎜
由于在内壁上有压力存在,故弯曲和变形也是存在的,只能在安全的基础上保证更经济。这里在危险截面处增加15㎜,通过弯矩图可知靠近边缘变形越小,为了节省材料,将主阀体端面设计为弧线。
3 结论
图11 第二次优化后的位移分析图 图12 第二次优化后的应力分析图
通过在Ansys软件中的分析,找到了防喷器主壳体的薄弱环节,即阀腔与闸板轨道相惯处,其原因是应力集中引起的。为了减小应力集中最佳的方法就是将其圆弧处理,不仅能解决问题,更重要的是实际的生产加工也很容易实现。由于有倒角的存在,使力分解到了椭圆形孔内壁,用Ansys分析后发现在闸板体轨道上出现了最大位移,再用弯曲变形公式进行计算得出在危险截面处增加壁厚15㎜。优化前最大位移0.04861㎜、最大应力132.145N;优化后最大位移0.030564㎜、最大应力90.143N。二者相对比之后可以看出采用的改进方法取得了良好的效果。
可以看到,我们运用有限元方法对关健受力构件进行应力分析,通过建模、分析,得到了构件的应力分布图、应力集中点及最大、最小应力值,通过力学知识和经验对应力结果进行综合分析,对构件的结构进行了改进和优化,消除了构件上的应力集中点,降低了构件最大应力值,获得了满意的设计结果。另外,通过有限元分析的结果来指导我们的设计,一方面可提高设计的可靠性和安全性,另一方面也提高我们的设计水平。
参考文献
[1] 韩松.防喷器试压控制系统的研究与开发[D].西安交通大学.2002.
[2] 由美雁.基于ANSYS软件的减速器建模与有限元分析[D]东北大学.2003.
[3] 李黎明.Ansys有限元分析实用教程.清华大学出版社
[4] Pro/E2001中文版.人民邮电出版社
[5] 陈凤棉.压力容器安全技术.化学工业出版社
收稿日期:2006—12—01
作者简介: 杨长青(1976—),男,西安工业大学机械设计制造专业研究生。
王琨琦(1955—),男,西安工业大学机电学院教授,主要研究方向为:D/CAM/CNC、传感器与测试技术。
单闸板防喷器主壳体的有限元分析及结构优化
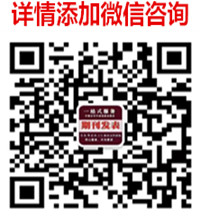